As a Supplier Conduct Quality Inspections?
June 25, 2025
How Do We, as a Supplier, Conduct Quality Inspections?
As a supplier, we understand that product quality is the cornerstone of customer satisfaction and trust. To ensure that every product meets or even exceeds customer expectations, we have established a rigorous quality inspection system. Below are the specific practices we follow in quality inspection:
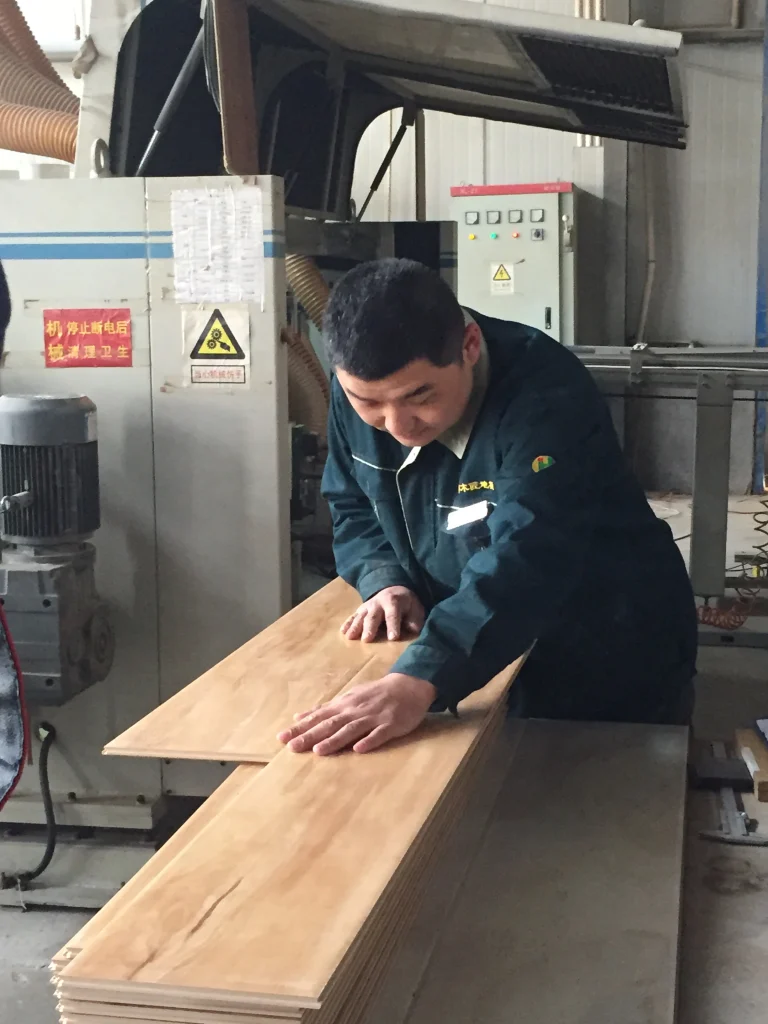
1. Setting Clear Quality Standards
At every stage of production, we have established clear quality standards. These standards are based on industry regulations, customer requirements, and our own experience, covering aspects such as materials, dimensions, performance, and appearance. We ensure that all employees are familiar with and strictly adhere to these standards.
2. Raw Material Inspection
Quality inspection starts at the source. We conduct strict inspections on all incoming raw materials to ensure they meet our quality standards. Only materials that pass the inspection are allowed into the production line. For critical materials, we also require suppliers to provide relevant quality certifications and test reports.
3. Production Process Monitoring
We implement full-process monitoring during production. Each production stage has dedicated quality inspectors to ensure that products meet requirements at every step. We use advanced inspection equipment and technologies, such as automated inspection systems and real-time data monitoring, to improve accuracy and efficiency.
4. Sampling Inspection
During mass production, we conduct regular sampling inspections. By randomly selecting samples, we can comprehensively assess product quality. If any issues are detected, we immediately halt production, investigate the cause, and make corrections until the problem is fully resolved.
5. Comprehensive Finished Product Testing
After production is completed, we conduct comprehensive testing on finished products. This includes visual inspections, functional tests, durability tests, and more. We also simulate real-world usage environments to ensure products perform reliably under various conditions. Only products that pass all tests proceed to packaging.
6. Third-Party Inspection
To ensure the objectivity and authority of inspection results, we invite third-party inspection agencies to conduct independent tests. The reports provided by these agencies not only offer valuable improvement suggestions but also enhance customer confidence in our products.
7. Customer Feedback and Continuous Improvement
We highly value customer feedback. Whether it’s positive reviews or constructive suggestions, we take them seriously. By analyzing customer feedback, we can identify potential quality issues and continuously optimize our production processes and quality inspection systems.
8. Employee Training and Quality Awareness
We regularly provide employees with training on quality management and inspection techniques to ensure they are equipped with the latest knowledge and skills. Additionally, we reinforce quality awareness among all staff through internal communication and incentive mechanisms, ensuring everyone understands the importance of quality inspection.
9. Records and Traceability
We have established a comprehensive quality record and traceability system. Detailed records are kept for each batch of products, including production data, inspection results, and corrective actions. If customers encounter any issues during use, we can quickly trace the source of the problem and provide effective solutions.
10. Continuous Optimization of the Quality Management System
We continuously learn from and adopt international best practices in quality management to optimize our system. By implementing international standards such as ISO9001, we ensure that our quality inspection processes are more systematic and standardized.
As a supplier, we always prioritize quality inspection. From raw materials to finished products, from production processes to customer feedback, we ensure that every product meets the highest standards through a strict quality control system. We believe that only by maintaining high quality can we earn customer trust and build long-term partnerships. In the future, we will continue to strive for excellence, constantly improving our quality management practices to provide customers with even better products and services.